How to create a Telecom Inventory
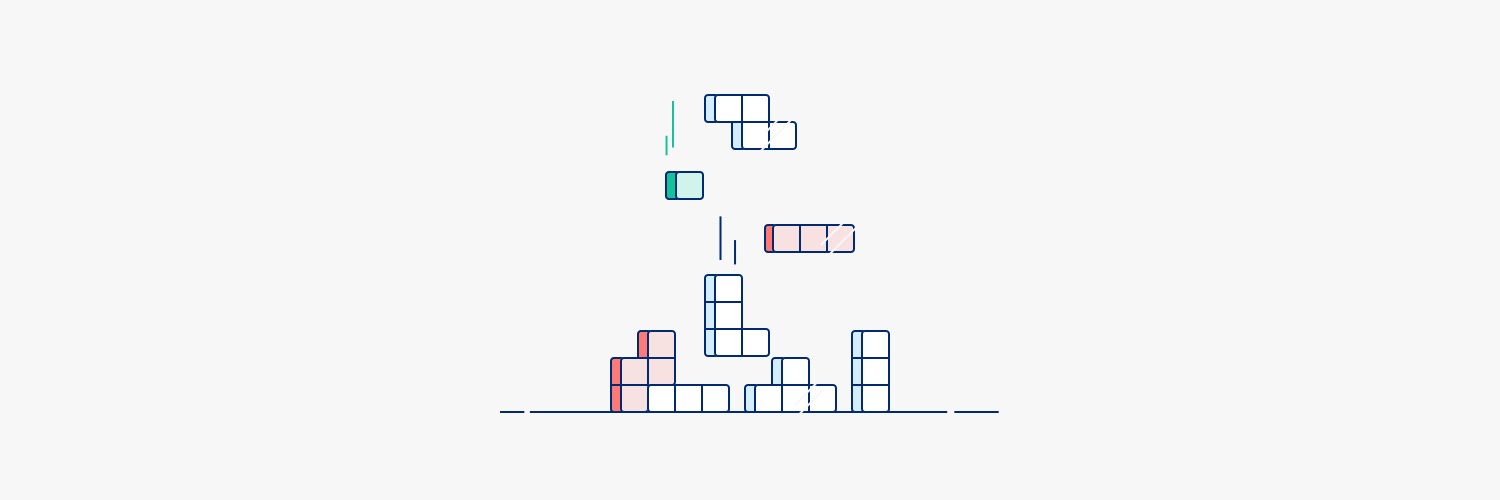
In the world of inventory management taking a step back to reflect on what inventory information you’re managing is useful.
In regards to telecom inventory, the inventory collection should be a stock pile of your organization’s telecom assets accumulated as a result of your network projects related to your business’s domestic, regional or global IT network footprint. In layman’s terms, your telecom inventory should be a complete list of your network.
However, the important key aspects here are understanding what information should be captured, how to structure the information so it can be accessed later and for what purposes this information will be used for.
Here’s a free template on how to create a telecom inventory
Check out how to manage inventory in Temforce
Information Gathering
Most organizations have some form of this information spread across many different teams and sources.
For example, the procurement team, captures commercial information perhaps in emails or in excel which contain vendor quotes, or within an internal contract database. The service delivery teams have a summary of the network assets captured and stored in an access database, spreadsheets or project docs, the NOC team has a wide arsenal of tools which are tracking the network up time and overall performance of the network which fingers crossed, have all been mapped correctly such that when there’s an outage John can troubleshoot the network and bring services back into production.
Typically, it’s during moments of crisis that your inventory management becomes crystal clear whether or not you’re in good shape when it comes to your internal systems and how the information has been captured across various sources.
For example, the minute you lose that connection that your board which includes your CIO was using for a boardroom video and the NOC is struggling to identify the Service ID to raise an outage, that’s when you know it’s about to hit the fan.
It’s usually now when your CIO picks up the phone to the head of the NOC and says fix it so this never happens again. Or when your CFO is in a meeting with the head of IT finance and your cost have just spiked $3M from last month and the head of finance has a song and dance about why these costs weren’t forecasted or accrued for last month.
A lot of the problems that arise because of bad or lack of inventory management can be solved with good practices or rules around how and what information will be captured associated with your business’s inventory.
Establishing a Solid Inventory
One of the keys to establishing a solid inventory is to start with what how an inventory element is generated and to identify the teams involved in this process.
Your business demand (Moves, Adds, Changes, Disconnects a.k.a MACD) IT projects associated with opening a new office, replacing equipment, connecting to a third party manufacturing plant etc. Whether you have one individual responsible for this process or a team, put some controls in place and perhaps even policies in place around this process.
Develop an agreed approved workflow for example, for product X, engineering must design and approve the solution, procurement must go to market and raise quotes or add pricing from the contract, finance must either be notified or approve the request prior to ordering and Jenny from service delivery is responsible for configuring the network or delivering the iPhone to the end user.
This might sound like a lot of unnecessary bureaucracy or red tape but getting everyone on the same page upfront saves a lot of headache later. As various Service Types i.e. Data, Voice, Mobile, Trader Line) are ordered, think though what information is important to capture and ensure the *must have fields are completed and not just with 1234 or abcd just to fill in the blanks.
The data quality you capture up front will make or break your inventory repository later.
Don’t be afraid to push back holding yourself and other people accountable for providing you with complete and accurate information is what’s important.
A defined process or policy quickly identifies where the process worked or is broken such that the next time your board room video is down or finance head is meeting with the CFO the team will either be on their A game because all the information they require is at their fingertips or can go back and review the workflow and identify that Tom entered 123 as the service ID and now they have some explaining to do.
Helpful Tip: Standardization of the information is critical. For example use agreed, location codes to refer to offices so you don’t end up with 10 locations with variations of the same address or 5 product names for the same product type.
Bad inventory or lack of an updated inventory is the stuff that shouldn’t keep you up at night wondering what kit is end of life and about to fail next, or whether your month end process is going to go smoothly because you have the confidence your team has reconciled the invoices correctly and are ok to be paid or sweating bullets because your CPO has just given your team a challenge of bringing down your Telecom cost by 25% yet you haven’t got a clue what telecom services you have, who they’re with, what services are up for renewal, are your cost in line with the market etc. etc.
Here’s a free template on how to create a telecom inventory
The Essential Inventory Management List
We’ve included a list of a few key areas to capture across your inventory as some food for thought to consider as you build up your inventory whether it be in a solution like temforce which automates this entire process or in a bespoke solution ridge together with hopes and dreams it’s correct.
Product Name i.e. MPLS, Leased Line, VOIP, PSTN, Mobile Device, EI, PRI
Service Type – Data, Voice, Mobile, Audio Conferencing, Trader Line
Capturing information is key for:
- Ensuring the order is accepted by carrier
- Asset End Of Life identification
- Financial forecasting purposes
- Outage purposes
- Understanding what cost center to allocate the cost to internally
What to Inventory and track
- Service ID’s (circuit ID, phone number) both the internal and carrier reference
- Equipment SLA
- Internal approval – who signed off on the design or spend?
- Carrier Routing diagrams
- Install start and end dates
- Carrier quotes – leverage for benchmarking your cost
- Internal project codes
- Location A & B
- Copies of order forms
- Parent Child relationships
- Carrier account information
- Demarc – where is the service physically installed, room, floor jack etc
- Router name
- IP address Information
- MPLS QOS profile
- Capacity \ Bandwidth
- Purpose – i.e. Boardroom video, elevator, modem
- Local loop provider
- ASN
- Physical Interface
- Cross connect information
- Site contact information
- Financial Cost Centers and G/L Codes
Cost
Broken down by components: i.e. access, port, QOS, router, local loop, device, plan, usage, VOIP channel, voice CPM
Mobile type
- Provider
- Plan
- Device Type
- SIM
- EIM
- ESN
- PUK Code
- Phone number
- Usage
Discover more about temforce’s approach to inventory management.
How to create a Telecom Inventory
Inventory management and creating a centralised repository
How to Maintain an Accurate IT and Telecom Inventory
Here’s a free template on how to create a telecom inventory
Check out how to manage inventory in Temforce
Temforce is a Technology Expense Management SaaS that simplifies maintaining your inventory, spend and suppliers without the hassle of spreadsheets.
If you’re interested in learning more about Temforce invoice validation contact us
Temforce – #1 Technology Expense Management SaaS